Inside of a plastic pyrolysis plant, waste plastic items are processed into commodifiable materials like fuel oil. In the modern world, it’s not unrealistic to think that over a third of all trash comprises of recyclable plastic items such as straws, juice containers, coffee cups, bottles, packaging, etc. Given that plastic-based materials can take hundreds of years to decompose naturally, it’s clear to see how sending such items to landfill sites is only going to create huge environmental problems. As a consequence, many countries are now promoting the use of pyrolysis technology (proceso pirolisis) to convert plastic waste into fuel oil. Some of the regions where plastic pyrolysis plants for sale are most sought-after include Norway, South Africa, Brazil, South Korea, Germany, the UK, Indonesia, and the Philippines.
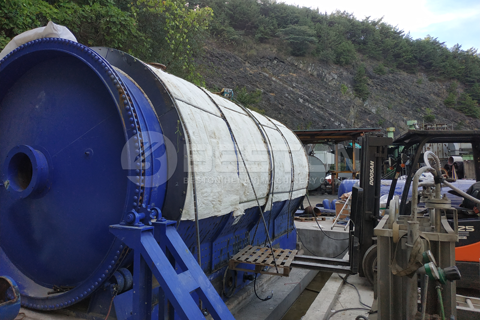
In a bid to fulfill the specifications of different clients, plastic pyrolysis machine suppliers have designed various reactors with varying methods of working. The three main working methods of mainstream plastic pyrolysis plants for sale are fully continuous, semi-continuous, and batch. Despite the three main categories of machines, it’s important to note that plastic pyrolysis plants can be completely customized to fulfill the unique demands of any customer. The fully continuous pyrolysis reactor option is obviously the best choice for waste plastic management facilities that need to process hundreds of tons of raw waste materials each week: https://www.bestongroup.es/la-instalacion-de-pirolisis-de-plasticos/.
The stated daily processing capabilities of mainstream waste plastic pyrolysis reactors range from around 5 tons to 24 tons. What’s more, most reactors can deal with all manner of raw materials, including rubber, car tires, oil sludge, and various types of agricultural waste. Pyrolysis reactors can generally be heated using a range of fuels including charcoal, natural gas, LPG, fuel oil, diesel, wood, and coal. Just about all reactors in plastic recycling plants employ water cooling methods, and each reactor has a working lifespan of between half a decade and eight years.
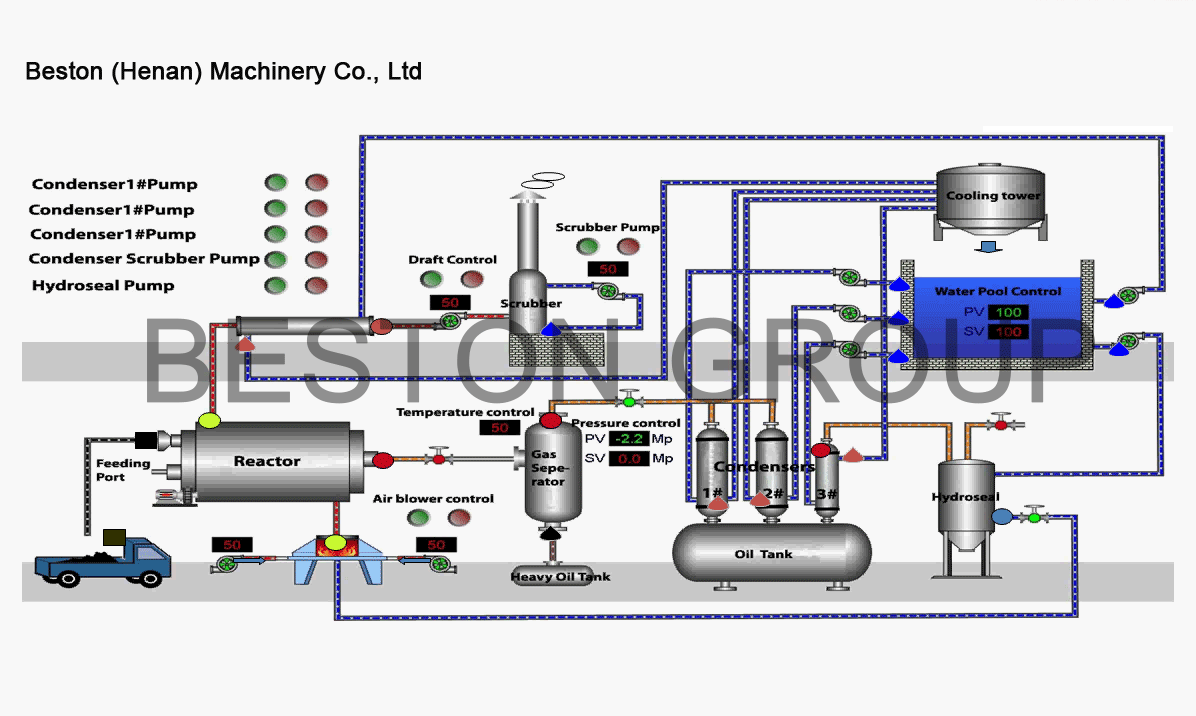
When it comes to stating the pressure under which different plant types operate, one should know that fully continuous and semi-continuous plants operate under consistent pressure, whereas batch system based plants operate under everyday pressure. The two automatic models have horizontal reactors, while batch system plants utilize rotary reactor technology. Despite the large investment cost of plants with horizontal reactors, it’s important to note that such reactors are much more energy efficient, so running costs are optimized: bestongroup.es.